"Add this many shots after this many hours in service" instructs the motor plate. And away went the lube tech, blindfolded, grease gun in hand, oblivious to the destructive potential of his actions. Don't blame him. He's doing his job the best way he can.
The problem is not the lube tech, it's the philosophy that gave birth to his bad practices and the less than excellent culture that allows them to continue.
Why complicate lubrication with calculators designed to estimate grease replenishment quantities, and calendars designed to estimate grease replenishment intervals? Especially when these calculations return invalid answers that destroy assets and profits.
Let's review what Goldilocks discovered.
- Add too much grease, and bearings enter a churning phase that produces high friction.
- Add too little grease, and there's no separation of components, also producing high friction.
- Add just the right amount, and bearings enter the bleeding phase where friction levels are low.
The common denominator in these three scenarios is FRICTION.
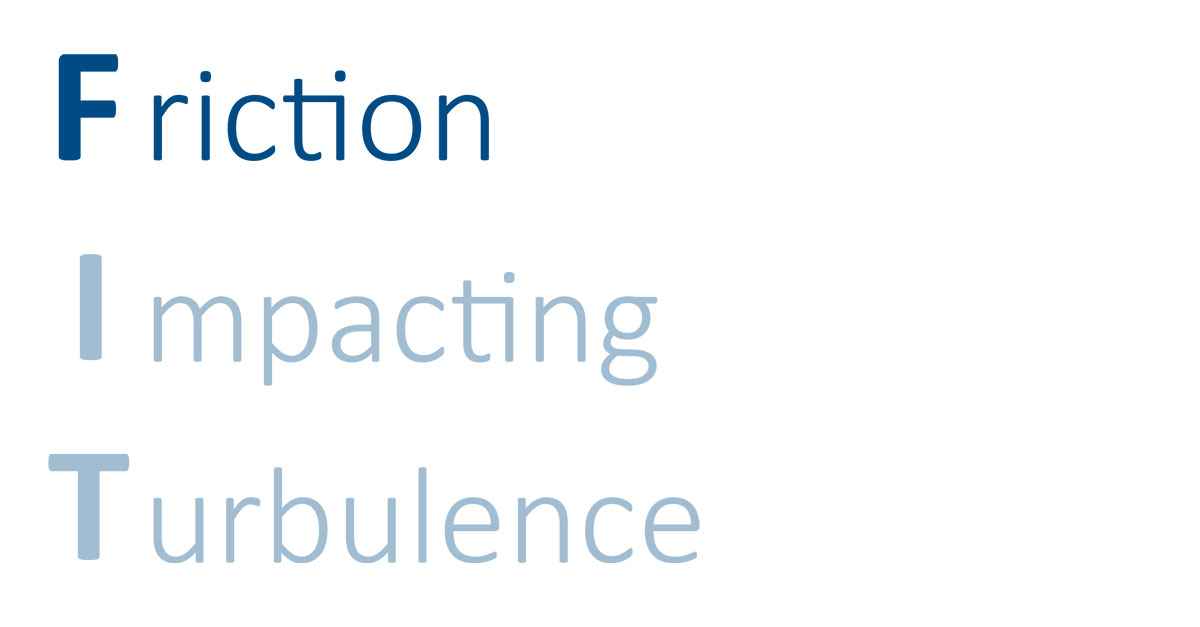
And we now know that the best technology to monitor, measure, and trend friction is ultrasound.
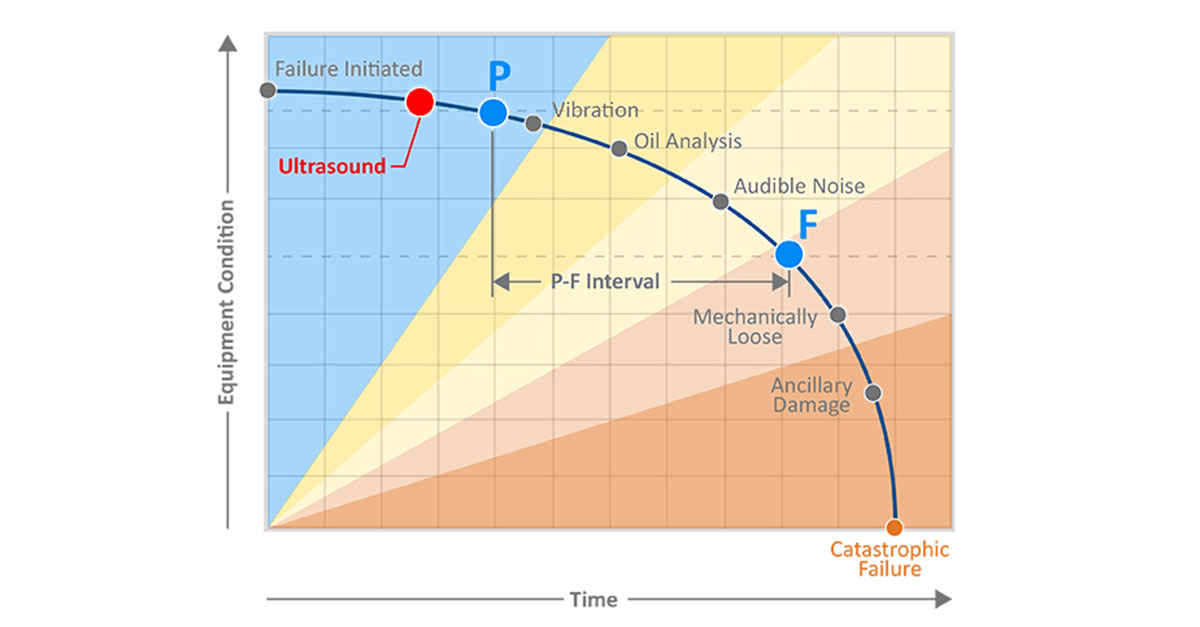
Training cannot overcome poor, or lack of tools. Good procedures are not enough. Lube technicians need the right tools, and they need to be trained on how those tools interact with their organization's goal to achieve precision lubrication.
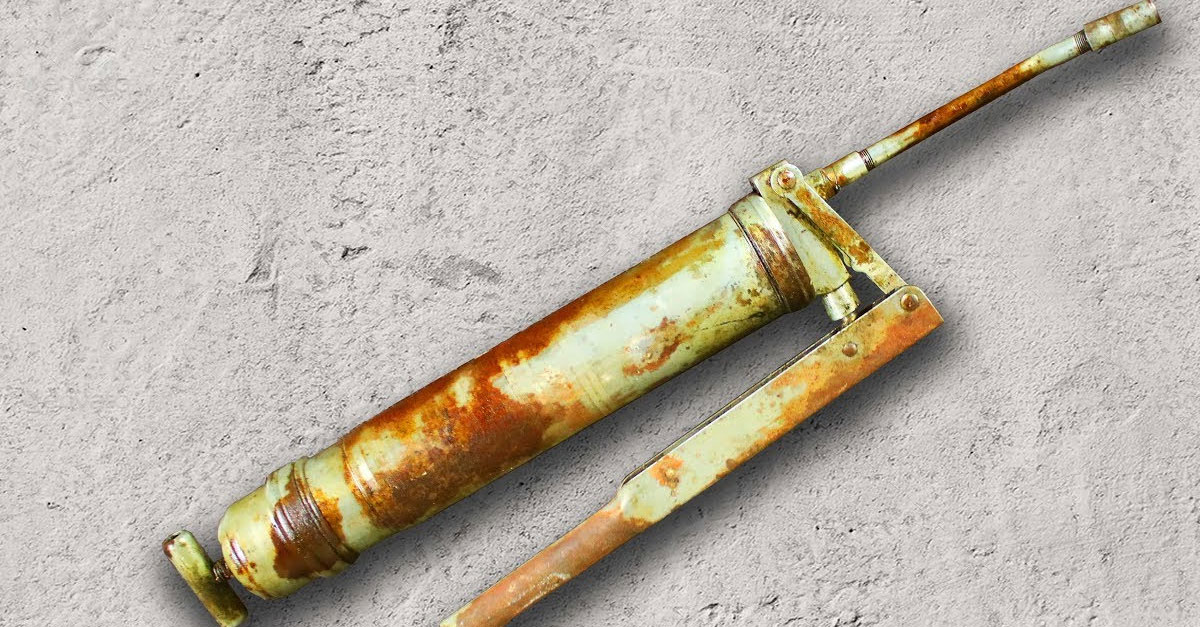
Yesterday, the best they might have had is a calendar and a calculator. Are these the best tools to achieve precision lubrication? They might have been at one time. This might even have passed for leading edge thinking. But it wasn’t right then, and its surely wrong today.
When a trained lube tech measures the effect every shot of grease has on the friction levels in a bearing, he knows when to start, when to stop, and exactly what quantity of grease is required to restore optimum friction. When a trained lube tech achieves lubrication excellence, he becomes a LUBExpert.
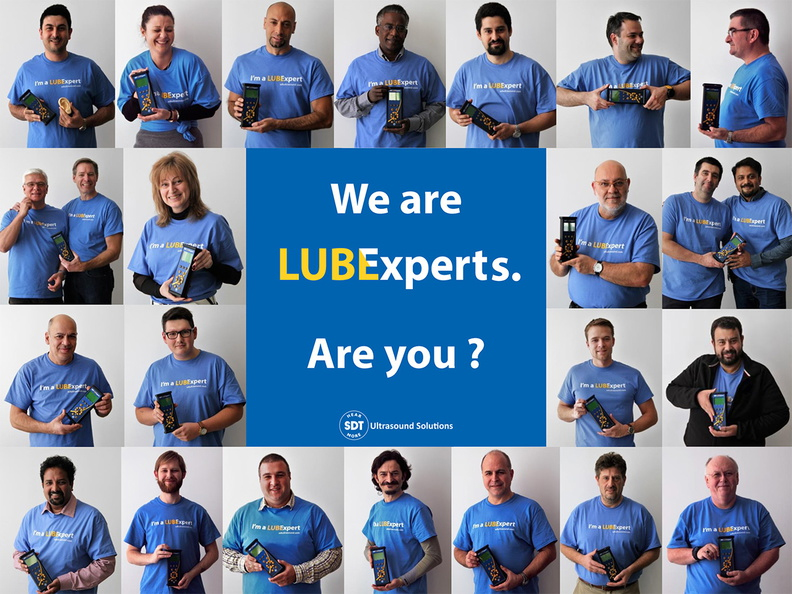
Read the previous post in this series, How Grease Works...Read More